Carbon Footprint
Global warming potential (GWP), commonly known as a ‘carbon footprint’, measures the potential global warming impact of a process in CO2 equivalents of greenhouse gases between a defined start and end point. Different emissions can have a lesser or greater global warming impact so, for convenience, they are measured and then converted into ‘CO2 equivalents’ of greenhouse gases. For instance, one tonne of methane has the equivalent global warming impact of twenty five tonnes of carbon dioxide.
At Futamura, we have in-house Life Cycle Assessment (LCA) capability, backed up by external expertise from thinkstep. In the case of NatureFlex™, a complete LCA has been carried out from ‘Cradle to Gate’; this has allowed us to measure and understand the impacts of all our raw materials, through the whole of our manufacturing process until the finished slit reel of film is ready to leave our site.
Significant improvements have been made to the raw materials we employ and to our manufacturing process, including a new production line that started-up in 2009. This has resulted in the most recent product carbon footprint of a NatureFlex™ film being only 43% of the level of a Cellophane™ film in the 1990’s. This improvement will continue, with further investment in our process and product portfolio.
GLOBAL WARMING POTENTIAL 2014
(kgCO2eq/kg)
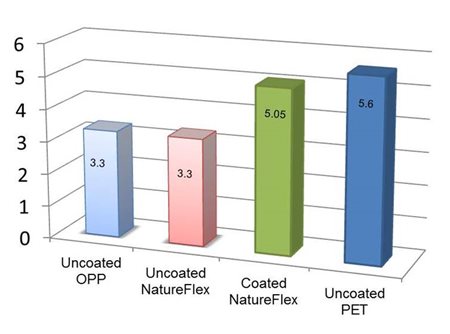
Sources: Independently reviewed Futamura LCA data. BOPP and BOPET data from PlasticsEurope. All data is modelled using GaBi software and includes biogenic CO2
It is increasingly common for companies to seek to compare the carbon footprints of different materials, but great care must be taken to ensure that the comparisons are made only between materials with similar functional properties and using the same LCA methodologies and start and end points.
The graph shown above compares the latest carbon footprint values (kg CO2eq / kg) of plain, uncoated NatureFlex™ and of barrier-coated NatureFlex™ films with that of a basic BOPET film. These films represent the closest comparative materials in terms of density, mechanical properties, printability and heat resistance and therefore serve similar market applications. For reference, an uncoated BOPP is also shown.